Embarking on a digital transformation journey can be daunting, especially for small and medium-sized manufacturers. Drawing from the insights gained through hundreds of MRP software implementations and the valuable input of our user base of device and equipment manufacturers, we’ve identified over 100 common problems that can derail your efforts.
This ultimate guide not only highlights these pitfalls but also offers practical strategies to overcome them, ensuring a smoother transition to digital excellence. Our hands-on implementation process can help you overcome all of these issues and give you added confidence in your digital transformation journey.
Contents
- Budgetary Issues
- Change Management
- Vision and Strategy
- Training and Skills
- Project Management
- Data and Security
- Integration and Compatibility
- Infrastructure and Support
- Vendor and Software Selection
- Communication and Collaboration
- Performance and KPIs
- Regulatory and Compliance
- Process and Workflow
- Testing and Quality Assurance
- Conclusion
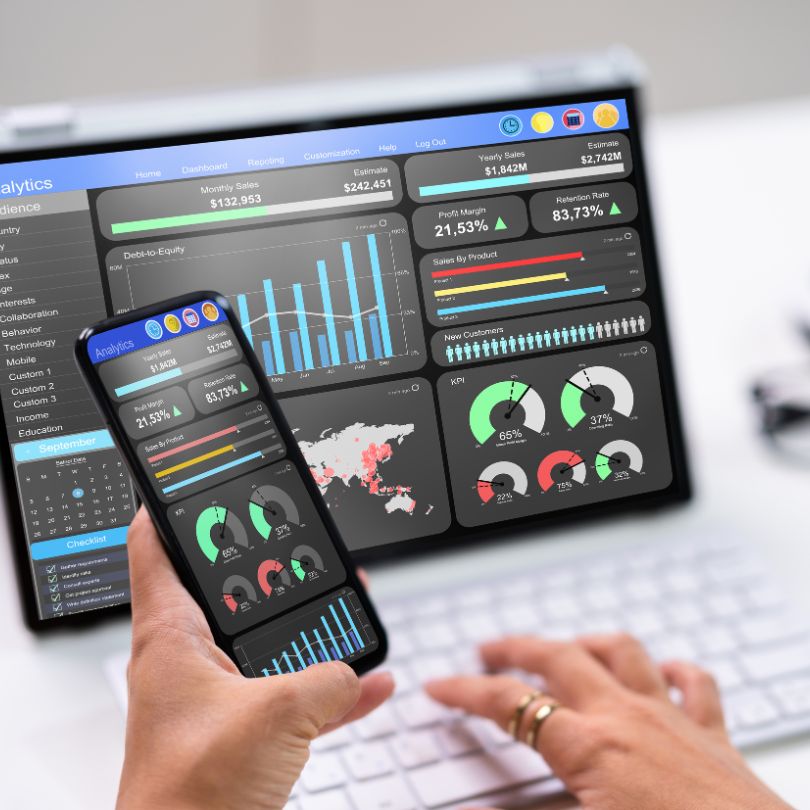
Budgetary Issues
1. Inadequate Initial Funding: Insufficient initial funding for MRP software implementation can lead to incomplete projects and unmet goals, preventing the full benefits of digital transformation for SME manufacturers.
2. Budget Overruns: Costs exceeding the planned budget for new digital systems can strain financial resources, causing delays and disruptions in production and manufacturing operations.
3. Unrealised ROI: Failing to achieve the expected return on investment from manufacturing software can make the digital transformation seem unjustified, leading to stakeholder dissatisfaction.
4. Over-reliance on Consultants: Depending too much on external consultants can be costly and might not build internal capabilities, leaving the company vulnerable in the long term.
5. Hidden Costs: Unanticipated expenses, such as software licensing fees, hardware upgrades, and maintenance costs, can escalate the total expenditure, derailing the project.
6. Underestimating Long-term Costs: Not accounting for ongoing costs, including updates, support, and training, can lead to budget shortfalls and project stagnation.
7. Poor Financial Management: Lack of proper financial controls and monitoring can result in misallocation of funds and inefficient use of resources.
Strategies for Success:
– Thorough Budget and Project Planning: Establish a detailed budget and project plan, ensuring realistic timelines and continuous monitoring to stay within financial limits and meet deadlines.
– Set Realistic Expectations: Align project goals with budgetary constraints to ensure feasible returns from the new systems. Regularly assess the performance of your new MRP software to ensure it meets financial expectations.
– Build Internal Capabilities: Invest in training and developing internal teams to reduce reliance on consultants for ongoing product training and quick fixes.
– Identify and Plan for Hidden Costs: Conduct a comprehensive cost analysis to identify potential hidden expenses and plan for them in the budget.
– Plan for Long-term Costs: Include provisions for ongoing costs such as updates, support, and training in the budget to ensure sustained success.
– Implement Robust Financial Controls: Establish strong financial management practices to monitor and control the allocation and use of funds effectively.
Change Management
8. Shopfloor Resistance to Change: Production operatives may resist new processes or tools potentially feeling insecure about the viability of their position if greater efficiencies are achieved or simply feeling threatened by the concept of ‘process automation.’ This can slow down the implementation of any new production management software and hinder productivity improvements.
9. Resistance from Middle Management: The introduction of MRP systems or CRM packages may threaten or overwhelm middle managers, impacting their support for the transformation.
10. Poorly Managed Expectations: Unrealistic expectations about the benefits of systems such as production management software or inventory software can lead to disappointment and reduced morale among employees.
11. Insufficient User Adoption Strategies: Without proper strategies, user adoption of any new system can be slow and ineffective, leading to underutilisation of the tools.
12. Overemphasis on Technology Over Process: Focusing too much on technology and not enough on improving underlying processes can limit the effectiveness of digital transformation efforts.
Strategies for Success:
Engage, Reassure, and Educate: Involve employees in the change process and provide adequate training on new systems to ensure smooth transitions. Ensure your team knows that the motivator for this change is improving quality and expanding the business, not reducing headcount. Freeing your team from repetitive tasks or duplicated work will allow them to do higher-level, more rewarding work!
– Align with Company Values: Ensure digital changes, such as implementing materials resource planning software, are in harmony with the company’s culture and values. Emphasise how these changes can improve production management and overall efficiency.
– Clear Communication: Set realistic expectations and communicate the benefits and goals of digital transformation to all stakeholders to ensure buy-in and support.
Vision and Strategy
- Lack of Clear Vision: Without a clear vision, digital transformation efforts can lack direction, resulting in fragmented initiatives and wasted resources.
- Misaligned Organisational Objectives: Objectives that don’t align with the company’s overall goals can waste resources and undermine the success of any MRP implementation. For example, if the primary goal of the company is to improve customer satisfaction but the MRP implementation focuses solely on cost reduction, the disconnect can lead to missed opportunities for enhancing customer experiences, thereby not fully realising the benefits of the transformation. Additionally, pursuing digital transformation without aligning it with broader business strategies, such as market expansion or innovation, can result in isolated efforts that do not contribute to the company’s long-term success.
- Misaligned IT and Business Strategies: Disconnect between IT and business strategies can lead to conflicting priorities and choosing the wrong software solution.
- Lack of Continuous Improvement: Failing to continually monitor, adapt, and improve can make the digital transformation obsolete, reducing the effectiveness of new systems.
- Lack of Innovation: Stagnation in innovation can hinder competitive edge and growth, limiting the benefits of digital tools.
Strategies for Success:
– Define Clear Objectives: Establish a clear vision for digital transformation and ensure all objectives align with business goals, including the effective use of MRP software and inventory management tools.
– Foster Innovation: Encourage a culture of continuous improvement and innovation to maximise the benefits of production management software and materials resource planning software.
– Integrate IT and organisational strategy: Ensure IT and business strategies are in sync for a unified approach to digital transformation.
Training and Skills
18. Siloed Training: Skills and knowledge naturally ‘pool’ around specific people in an organisation but allowing this to happen can leave you back in the position you were in before you implemented a new MRP system – with specialist knowledge held by a few people and your business left vulnerable when those people leave the business unexpectedly.
19. Insufficient Initial Training: Lack of training can lead to poor uptake in the use of new tools and processes, hampering productivity gains.
20. Lack of Skilled Personnel: A shortage of skilled staff can hinder the transformation process and the effective implementation of new production or manufacturing management software.
21. Underestimating Training Needs: Failing to recognise the extent of training required for MRP systems and new inventory management systems can result in unprepared staff and underutilised tools.
22. Insufficient Legacy System Knowledge: Lack of understanding of existing systems can complicate integration with new manufacturing software, causing delays and errors.
Strategies for Success:
– Invest in Training: Provide comprehensive training programmes to ensure staff are well-prepared to use any MRP software and specific functionality such as job cards or bills of material effectively.
– Hire and Develop Talent: Focus on hiring skilled personnel and developing existing staff to support the digital transformation.
– Assess Training Needs: Regularly assess and address the training requirements of your team to ensure optimal use of your manufacturing software and processes.
Democratise System Knowledge: Regularly review who is using your MRP system and look to rotate personnel across various roles (where possible) so more people can understand the various functions of your manufacturing software.
Project Management
23. Poor Project Management: Ineffective management of MRP system implementation can lead to missed deadlines and overspending, affecting overall project success and operational efficiency.
24. Unrealistic Timelines: Setting timelines that are too tight for the implementation of manufacturing software can cause stress and lead to poor outcomes, compromising the quality of the digital transformation.
25. Scope Creep: Allowing the project scope to expand uncontrollably can lead to delays and budget overruns, which can impact the rollout of materials resource planning software.
26. Underestimating Complexity: Failing to recognise the complexity of implementing MRP systems can result in insufficient planning and execution, leading to potential project failure.
27. Change Management Failures: Underestimating the cultural shift required in digital transformation projects can disrupt the project and reduce efficiency
28. Needless complexity in Project Management: Creating an overly complex roadmap of transformation can make the entire process overwhelming for some members of your team and result in a lack of engagement.
29. Inadequate Project Governance: Lack of proper oversight can result in project failures and inefficiencies, affecting the deployment of manufacturing software.
30. Failure to Adapt to User Feedback Post-Implementation: Gathering feedback is one thing, but effectively implementing that feedback after the system goes live is quite another.
Strategies for Success:
– Effective Project Planning: Create detailed process maps with priorities, ‘quick wins’ and realistic timelines, and clearly define the scope of your project to ensure successful MRP system implementation
– Robust Governance: Lead from the front and establish strong project governance frameworks to ensure proper oversight of the manufacturing software rollout.
– Manage Change Effectively: Implement structured change management processes to handle changes smoothly and maintain project momentum, ensuring the effective use of inventory management software and materials resource planning software.
– Listen to feedback, implement it and communicate it: Ensure that feedback reaches the people who need to hear it and that people know that the feedback they have given has been heard and acted upon. If there is a reason it hasn’t been acted upon that should also be communicated. Feedback is essential for continuous improvement and nothing stops feedback like a wall of silence!
Data and Security
- Insufficient Data Migration Planning: Poor planning for data migration can result in data loss, corruption, or downtime during the transition to the new system.
- Data Security Breaches: Breaches can compromise sensitive information and damage the company’s reputation, making it crucial to consider the security of your digital tools.
- Data Migration Errors: Errors during data migration can lead to loss of critical information and affect the performance of inventory management software.
- Insufficient Data Quality: Poor data quality can result in inaccurate reports and ineffective use of materials resource planning software, hampering decision-making processes.
- Poor Data Governance: Lack of proper data governance can lead to inconsistencies and errors in the MRP system, impacting the reliability of manufacturing software and leading to trust issues within the team.
- Poorly Defined Data Ownership: Unclear data ownership can cause accountability issues and affect the reliability of materials resource planning software.
- Overlooking Data Privacy: Ignoring data privacy can result in compliance issues and damage trust in the company’s digital transformation efforts, affecting the use of inventory management software.
- Mismanagement of Digital Assets: Poor management of digital assets can lead to inefficiencies and underutilisation of digital tools such as job cards and BOMs.
- Insufficient Backup Solutions: Lack of robust backup solutions can lead to data loss and hinder the recovery of MRP systems, impacting business continuity.
- Inadequate Disaster Recovery Plan: An insufficient disaster recovery plan can result in prolonged downtime and data loss, affecting manufacturing operations and the use of production management software.
- Insufficient Network Security: Poor network security can expose the MRP system to cyber threats, compromising data integrity and operations.
Strategies for Success:
– Implement Robust Security Measures: Ensure MRP systems and manufacturing software are protected with strong security protocols to prevent breaches and data loss.
– Maintain Data Quality: Establish processes to ensure high data quality for accurate reporting and effective use of materials resource planning software and inventory management tools.
– Define Data Ownership: Clearly define data ownership to ensure accountability and reliability in the use of MRP software and other digital tools.
– Prepare for Disasters: Develop comprehensive backup solutions and disaster recovery plans to minimise downtime and data loss, ensuring continuous operation of production management software and other critical systems.
Integration and Compatibility
42. Integration Issues: Challenges integrating new with existing systems can lead to operational disruptions and inefficiencies, hindering the seamless flow of manufacturing processes.
43. Legacy System Incompatibility: Incompatibility with legacy systems can hinder the full implementation of new manufacturing software, causing delays and increased costs.
44. Insufficient Legacy System Support: Lack of support for legacy systems can complicate the integration process.
45. Insufficient Cloud Readiness: Not being ready for cloud-based solutions can limit scalability and flexibility. Cloud readiness involves ensuring that the company’s IT infrastructure, applications, and processes can leverage cloud technologies. In the most basic sense, do you have the variety of devices required to run your MRP software, and is there good Wi-Fi coverage (capable of running the required number of devices) on your shop floor?
46. Insufficient System Flexibility: Rigidity in the system can prevent it from adapting to changing business needs.
Strategies for Success:
– Ensure Compatibility: Evaluate the compatibility of new MRP software with existing systems to ensure seamless integration and efficient operation of inventory management software.
– Support Legacy Systems: Provide adequate support for legacy systems to facilitate smooth transitions and integration with new manufacturing software if necessary.
– Prepare for Cloud: Enhance cloud readiness to leverage the scalability and flexibility of cloud-based MRP systems, ensuring optimal performance.
– Maintain System Flexibility: Choose flexible materials resource planning software that can adapt to evolving business requirements, ensuring long-term usability and efficiency.
Infrastructure and Support
47. Insufficient IT Infrastructure: Inadequate IT infrastructure in terms of hardware, networking and IT Support can hinder the effective implementation of MRP systems and other manufacturing software, affecting productivity and growth.
48. Insufficient Mobile Support: Lack of support for mobile devices can limit accessibility and efficiency.
49. Insufficient Scalability: Limited scalability can prevent the MRP system from growing with the business, affecting long-term viability and operational efficiency.
50. Inadequate Scalability Planning: Failing to plan for scalability can lead to constraints and inefficiencies as the business grows and evolves, impacting the performance of manufacturing software.
Strategies for Success:
– Invest in IT Infrastructure: Ensure robust IT infrastructure to support the implementation and use of MRP systems and manufacturing software, improving operational efficiency.
– Enhance Mobile Support: Provide comprehensive support for mobile devices to improve accessibility and efficiency in using job cards and inventory management software.
– Offer Strong Technical Support: Establish reliable technical support to quickly address and resolve issues with materials resource planning software, ensuring continuous operation.
– Plan for Scalability: Develop scalability plans to ensure MRP systems can grow with the business and support long-term success, enhancing the performance of production management software.
Vendor and Software Selection
51. Vendor Lock-in: Dependence on a single vendor can limit flexibility and increase costs, making it difficult to switch or upgrade MRP software and other manufacturing tools.
52. Poor Vendor Selection: Choosing the wrong vendor can lead to subpar software and inadequate support, affecting overall system performance.
53. Incorrect Technology Choices: Selecting the wrong technology can result in inefficiencies and poor performance of manufacturing software, hindering digital transformation efforts.
54. Vendor Management Issues: Ineffective vendor management can lead to poor service and support for new systems, impacting operational efficiency.
55. Poorly Managed Contracts: Mismanaged contracts can result in unfavourable terms and conditions, increasing costs and reducing benefits.
56. Ignoring Vendor Roadmaps: Not considering the future development plans of vendors can lead to issues with system updates and long-term compatibility.
Strategies for Success:
– Avoid Vendor Lock-in: Evaluate multiple vendors to ensure flexibility and competitive pricing for MRP software and manufacturing tools, allowing for easier upgrades and changes.
– Select the Right Vendor: Choose MRP vendors with a proven track record and strong support options, ensuring reliable service and system performance.
– Choose Appropriate Technology: Ensure the technology aligns with business needs and enhances overall productivity.
– Manage Vendors Effectively: Establish strong vendor management practices to ensure reliable service and support for new system(s), maintaining operational efficiency.
Communication and Collaboration
57. Poor Communication: Ineffective communication can lead to misunderstandings and misaligned efforts in the implementation of MRP systems, impacting project success.
58. Failure to Communicate Benefits: Not clearly communicating the benefits of digital transformation can result in a lack of support and enthusiasm.
59. Unaligned Metrics: Success looks different to different departments in your company. Agree on the core statistics for each department and the organisation as a whole, and share these metrics with everyone so you can measure the right things to judge your success.
60. Insufficient Stakeholder Buy-in: Without stakeholder buy-in, digital transformation efforts may lack support and funding.
61. Unclear Roles and Responsibilities: Undefined roles and responsibilities can cause confusion and hinder the success of software implementation.
62. Lack of Feedback Mechanisms: Without feedback mechanisms, it’s difficult to assess the effectiveness of new MRP systems and make necessary improvements.
63. Insufficient Stakeholder Communication: Failing to communicate with stakeholders such as clients, suppliers or despatch partners can result in a lack of support and engagement, especially during the implementation process. The outputs from your company are more than just the products you make, they are the sales quotes, invoices, despatch notes and other system outputs that impact other stakeholders.
64. Insufficient Collaboration Tools: Lack of collaboration tools can hinder teamwork and the efficient use of inventory management software and job cards.
65. Lack of Cross-Functional Teams: Without cross-functional teams, efforts to implement MRP systems can be siloed and inefficient.
66. Lack of Agile Methodologies: The absence of agile methodologies can lead to inflexible and slow digital transformation efforts.
67. Ignoring Cultural Differences: In global implementations, failing to account for cultural differences can lead to misunderstandings and reduced effectiveness of the new system.
Strategies for Success:
– Enhance Communication: Improve communication channels to ensure clear and consistent messaging about your new systems and their benefits for manufacturing processes.
– Engage Stakeholders: Secure stakeholder buy-in by demonstrating the benefits and ROI of the new software, ensuring support and funding and ensure that the outputs from your new system meet the needs of your stakeholders.
– Define Roles and Responsibilities: Clearly define roles and responsibilities to ensure accountability and efficiency.
– Implement Feedback Mechanisms: Establish feedback mechanisms to continuously improve the use of the new systems.
– Provide Collaboration Tools: Equip teams with collaboration tools to enhance teamwork and the effective use of all functions of your new system.
– Form Cross-Functional Teams: Create cross-functional teams to ensure diverse input and efficient implementation of software systems, enhancing overall effectiveness.
– Adopt Agile Methodologies: Implement agile methodologies to increase flexibility and responsiveness in digital transformation efforts using manufacturing software.
Performance and KPIs
68. Poorly Defined KPIs: Without clear KPIs, it’s difficult to measure the success of new software such as MRP systems and CRMs, hindering performance evaluation.
69. Inadequate Performance Monitoring: Insufficient performance monitoring can lead to undetected issues and inefficiencies, affecting overall productivity.
70. Poor Resource Allocation: Inefficient resource allocation can affect the success and ROI of manufacturing software, limiting the benefits of digital transformation.
71. Lack of Continuous Improvement: Failing to continuously improve can result in outdated practices and reduced competitiveness.
Strategies for Success:
– Define Clear KPIs: Establish clear KPIs to measure the success and performance of manufacturing software, ensuring alignment with business goals.
– Monitor Performance Regularly: Implement regular performance monitoring to identify and address issues promptly.
– Allocate Resources Efficiently: Ensure efficient resource allocation to maximise the benefits of new software, supporting overall productivity and growth.
Regulatory and Compliance
72. Regulatory Compliance Issues: Failing to comply with regulations such as component traceability can lead to legal issues and fines in some industries
73. Failure to Meet Industry Standards: Not meeting industry standards can result in poor performance and reduced competitiveness of manufacturing software.
Strategies for Success:
– Ensure Compliance: Stay updated with regulations and ensure all new software complies with industry standards, avoiding legal issues and fines.
– Adopt Best Practices: Implement best practices to meet and exceed industry standards, ensuring optimal performance and competitiveness of materials resource planning software.
Process and Workflow
74. Poorly Defined Processes: Undefined processes can lead to confusion and inefficiencies in the use of MRP systems, hindering productivity in manufacturing operations.
75. Poor Documentation: Lack of proper documentation of new processes and workflows can make it difficult to understand and use new systems like materials resource planning software, leading to errors and delays.
76. Inadequate Change Controls: Weak change controls can result in unapproved changes that disrupt operations, causing inconsistencies and inefficiencies.
77. Poorly Defined Workflows: Unclear workflows can lead to inefficiencies and mistakes, affecting overall operational performance.
78. Inadequate Process Automation: Insufficient automation can result in manual errors and inefficiencies in manufacturing operations, limiting the effectiveness of new software.
79. Overcomplicated Workflows: Overly complex workflows can hinder the effective use of manufacturing software, reducing productivity and increasing error rates.
80. Lack of Process Standardisation: Inconsistent processes can lead to inefficiencies and reduced effectiveness, affecting overall business performance.
81. Poor Feedback Loop: Without a feedback loop, it’s difficult to identify and address issues with manufacturing software, hindering continuous improvement.
82. Underutilised Features: Not fully leveraging all features of the new MRP software can result in missed opportunities for optimisation and efficiency gains.
Strategies for Success:
– Define Processes Clearly: Establish clear and well-documented processes to ensure efficient use of systems.
– Improve Documentation: Provide comprehensive documentation to support the understanding and use of manufacturing software, reducing errors and delays.
– Implement Change Controls: Strengthen change controls to manage and approve changes effectively, ensuring smoother operations.
– Standardise Workflows: Standardise workflows to reduce inefficiencies and improve the effectiveness of materials resource planning software.
– Automate Processes: Increase process automation to reduce manual errors and enhance efficiency in manufacturing operations.
– Simplify Workflows: Simplify workflows to improve the usability and effectiveness of manufacturing software, enhancing productivity.
– Establish a Feedback Loop: Create a feedback loop to continuously identify and address issues, fostering continuous improvement.
Testing and Quality Assurance
83. Insufficient User Acceptance Testing (UAT): Lack of thorough User Acceptance Testing can lead to the software not meeting the real-world needs of the end-users, causing disruptions in manufacturing operations.
84. Inadequate Integration Testing: Failing to adequately test the integration of the MRP system with other existing systems can result in data inconsistencies and workflow interruptions.
85. Poor Data Validation Testing: Weak data validation testing can allow incorrect or corrupt data to enter the system, leading to inaccurate reporting and decision-making.
Strategies for Success:
– Conduct Comprehensive User Acceptance Testing: Engage end-users in testing to ensure the software meets their practical needs and functions correctly in real-world scenarios.
– Implement Rigorous Integration Testing: Test the integration of the MRP system with other business systems to ensure seamless data flow and operational harmony.
– Prioritise Data Validation Testing: Regularly validate data inputs and outputs to ensure accuracy and integrity, supporting reliable reporting and decision-making.
Conclusion
Navigating the complexities of digital transformation can be challenging, but by being aware of these common mistakes and implementing our recommended strategies, you can set your company on the path to success.
If you found this guide helpful, please share it with someone you know who is about to embark on their company’s digital transformation journey. For more insights and tips, be sure to follow us on social media, subscribe to our podcast ‘Made To Grow‘ and stay updated with the latest content from our experts.