An effective stock management process is one of the key components of a company’s purchasing efficiencies. Stock is a large capital investment so it makes sense to manage it as well as possible.
In particular, keeping track of raw materials is essential for the smooth flow of the production process. Internal controls to prevent loss, damage and misuse of stock must be established and maintained.
Depending on the type of business, these internal controls include:
Secure the Warehouse
Locked gates and doors with only authorised entry is the first step to securing the stock.
Organise the Stock
If you can’t find it, you can’t control it! Each stock item should be numbered as well as the location that it is stored in. This facilitates quick and easy tracking in the long run.
Read more about Flowlens Stock Management features and benefits.
Ready to Start Your Digital Journey?
We’ve analysed hundreds of successful MRP implementations, and in this FREE e-book, we break down the essential steps you need to follow to ensure your digital transformation is a success.
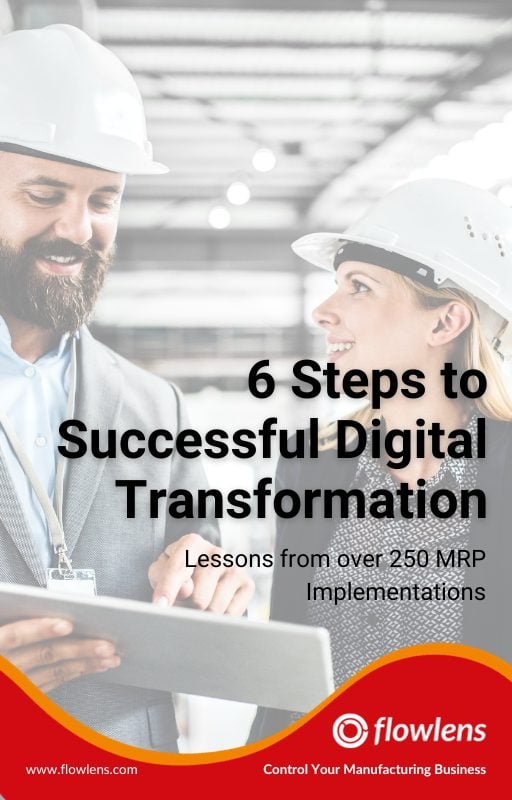
Count all Deliveries
Do not rely on delivery dockets. Identify who is responsible for signing off on the quantity received before it is officially recorded as ‘in stock’. If there are items missing or damages, this needs to be noted immediately and appropriate action taken, (accounts department notified, goods returned, etc.) Using an automated handheld scanner is the most error-free method of stock recording.
Tag all Materials
Each item should be identified by part number and description to avoid any confusion or the wrong part being used for the wrong production.
Standardise the Picking Process
Whether it is a manual or automated procedure, when any item leaves the warehouse for use in production, servicing, or otherwise, it must be recorded. A controlled gate or door is extremely beneficial for this step.
Check the Bill of Materials (BOM)
The Bill of Materials is a list of the parts needed for production and it is used to pick materials from stock. Ensure that your BOM software is reliable as this will save messy additional requests and returns at a later date.
Conduct Spot Checks
Compare small, frequent, manual counts of the warehouse stock with the recorded amounts and investigate any errors found.
Record all Wastage
If scrap materials are thrown away without being properly recorded, the stock management and accounting systems will assume that they are still in stock and quantities and values will be inaccurate. Create a procedure to record wastage regularly.
To see how Flowlens can help you control and manage your manufacturing process and stock requirement, book a demo today/